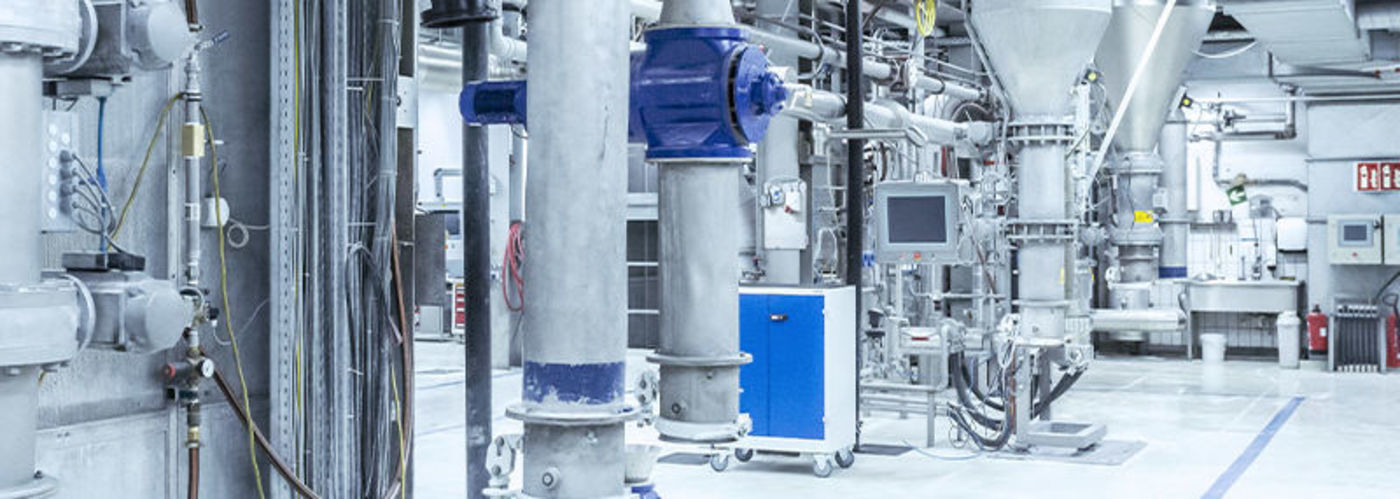
New test centre for battery applications
Hosokawa Alpine is building a test centre for various battery applications and materials, including the recycling of coated battery films. The first product tests are expected to be carried out from March 2025.
Test centre with the highest safety standards for critical materials
Some battery active materials are based on mineral raw materials, such as nickel-manganese-cobalt (NMC), which are expensive and sometimes have to be sourced via unsafe supply chains. To enable the reuse of these raw materials, the recycling of valuable battery materials is becoming increasingly important. This is also important from an environmental perspective in order to protect our natural resources. At the same time, long delivery routes are eliminated, which helps to reduce the CO2 footprint.
The market for battery recycling has high growth potential. One of the drivers is the EU battery regulation that came into force at the beginning of the year. Manufacturers of industrial and electric car batteries are therefore obliged to use recycled battery materials in the production of new battery systems. Special framework conditions are required for the recycling process of NMC battery materials. With the new ON product line and the associated focus on the battery sector, there was an urgent need for action: Hosokawa Alpine decided to set up a special test centre for the recycling of coated battery films. This is where the company presents innovative solutions for its customers in the battery market.
Process for recycling production waste during ongoing battery production
The new test center will house four machines from Hosokawa Alpine: the Rotoplex granulator for pre-cutting the battery electrode foils, the UPZ fine impact granulator and the AFG fluidized bed counter-jet granulator for fine grinding, as well as the Turboplex ATP ultra-fine air classifier. Hosokawa Alpine is using them to implement a process that allows production waste to be recycled during ongoing battery production. In the new test center, Hosokawa Alpine is testing how this process fits into customers' production processes and how they can make their battery production more efficient while meeting the prescribed recycling quotas. Hosokawa Alpine is carrying out tests with customers' materials in order to find the optimum solution for them - naturally with the highest safety standards for employees.
And the company is already looking further into the future: “At the moment, our focus is clearly on batteries. But the new technical center is equipped in such a way that other critical materials can also be tested and recycled there in future,” says Thomas Weischer, Vice President Business Development at Hosokawa Alpine.
Recommend article